Proton Exchange Membrane Fuel Cells (PEMFCs) operate at 60–80 °C, separating hydrogen into protons and electrons at the anode. Protons migrate through a polymer electrolyte membrane (PEM) and combine with oxygen and electrons at the cathode, producing only pure water as a byproduct. This direct electrochemical conversion delivers high electrical efficiency (> 50 %), rapid start-up and shutdown, and high-power density, making PEMFCs as attractive zero-emission power source for mobility applications such as automobiles, ships and urban air mobilities (UAMs).
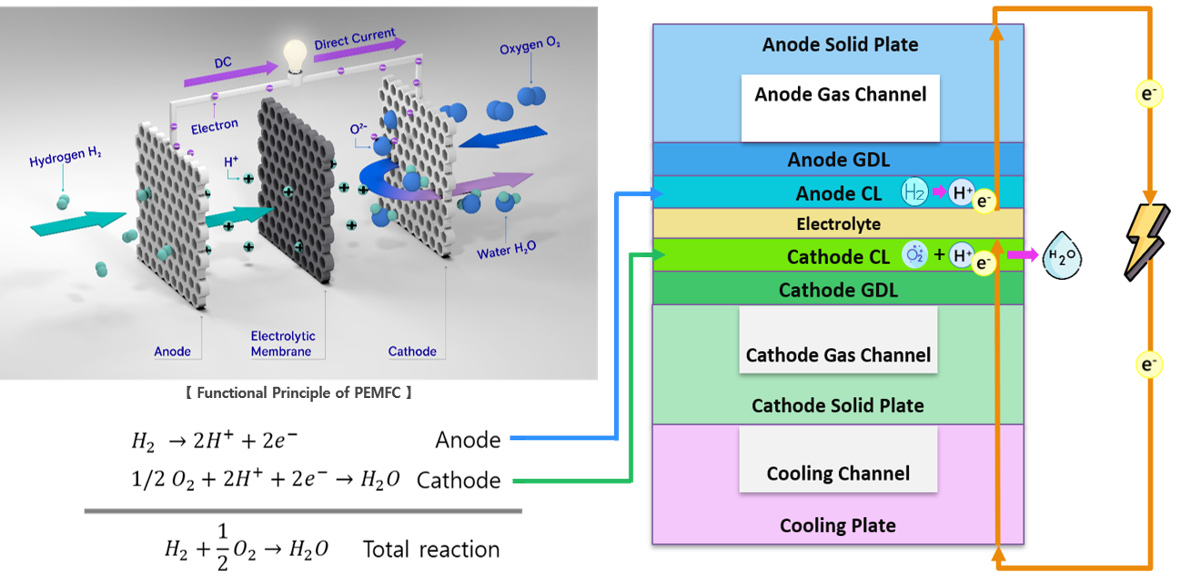
However, PEMFCs face several challenges for widespread adoption in mobility applications. The sluggish oxygen reduction reaction (ORR) incurs an overpotential of ~0.4 V, necessitating reliance on costly platinum-based catalysts. Furthermore, PEMFCs exhibit slower dynamic response than conventional internal combustion engines (ICE), and rapid load fluctuations in mobile platforms can accelerate stack degradation significantly. Therefore, integrating the PEMFC with energy storage systems (ESS) is essential to manage transient loads effectively. For the commercialization of the PEMFC-battery hybrid mobilities, water management and thermal management researches are required to reserve the long-term durability of the PEMFC systems. Furthermore, researches about optimal energy management system (EMS) of the PEMFC-battery hybrid system are also inevitable.
Our group addresses challenges of PEMFCs through advanced multiphysics modeling and simulations. We develop PEMFC system model consists of detailed PEMFC stack model and base of plant (BOP) models, and PEMFC -battery hybrid system model. The researches about the EMS for the PEMFC-battery hybrid system are also ongoing. Furthermore, we also do techno-economic analyses to estimate the feasibility of the PEMFC-battery hybrid mobility systems.
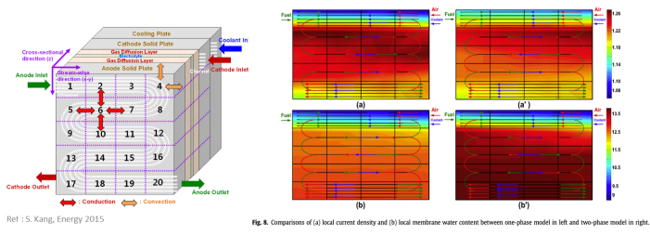
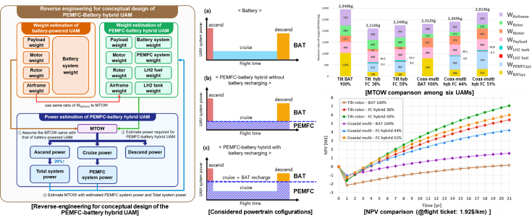
Solid Oxide Fuel Cells (SOFCs) are electrochemical energy conversion devices that operate at high temperatures—typically above 600°C—and are known for achieving the highest level of thermodynamic efficiency among all fuel cell technologies. One of the key advantages of SOFCs is their exceptional fuel flexibility. Their high operating temperature allows for the internal reforming of a wide range of fuels, including methane and ammonia, which provides significant advantages in terms of infrastructure scalability and economic feasibility. In addition, the high-grade waste heat produced by SOFCs can be effectively utilized in cogeneration systems or integrated into hybrid configurations with other thermal processes, thereby improving overall energy efficiency. These characteristics make SOFCs highly suitable not only for stationary power generation but also for diverse applications such as maritime propulsion and combined heat and power (CHP) applications.
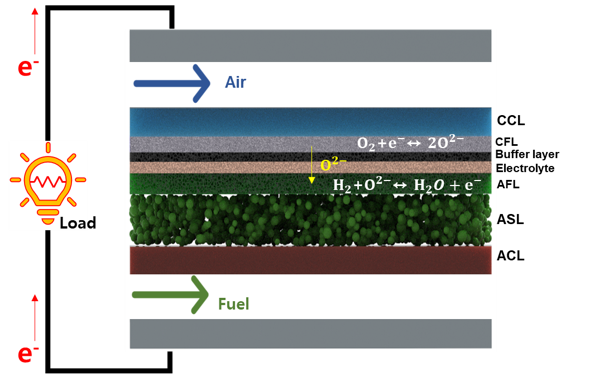
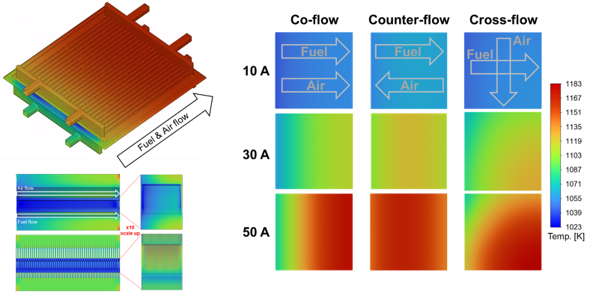
Our research on SOFCs is conducted at both the stack and system levels. In the stack analysis, thermal management emerges as a critical issue. Non-uniform flow distribution across the stack can lead to spatial gradients in temperature (e.g., cold spots and hot spots) and current density, which in turn may accelerate localized degradation and reduce the long-term durability of the cell. To address this, we perform multiphysics analysis using computational fluid dynamics (CFD) to investigate the coupled phenomena—such as fluid flow, heat transfer, electrochemical reactions, and mass transport—within the SOFC stack. Based on the findings, we propose optimized stack designs aimed at minimizing thermal and electrochemical non-uniformities. This stack-level modeling framework will be further scaled up to a hotbox-level analysis, enabling more realistic predictions of thermal behavior in full-scale SOFC modules.
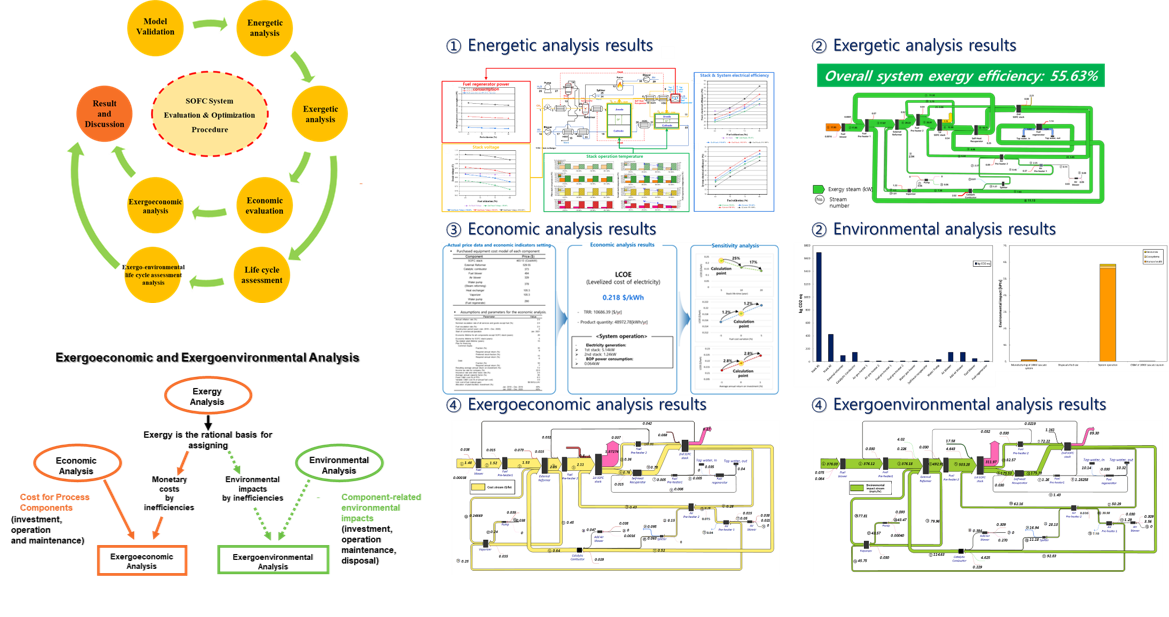
System-level analysis is categorized into two major types: steady-state analysis and dynamic analysis.
· In steady-state analysis, the primary objective is to propose the optimal system configuration. This optimization must simultaneously consider multiple performance metrics, including energy and exergy efficiency, economic viability, and environmental impact. To achieve this, we utilize advanced methods such as exergoeconomic analysis and exergoenvironmental analysis, which allow for a comprehensive evaluation of both energy and exergy flows in relation to cost and environmental emissions.
· In dynamic analysis, the focus shifts to understanding the transient behavior of the SOFC system in response to varying load demands, particularly in propulsion applications such as marine vessels. We analyze how both the SOFC stack and the balance-of-plant (BoP) components respond under real-time operational changes. The goal is to develop optimal control and operating algorithms that ensure system stability, efficiency, and responsiveness during dynamic operation.