PEM Water Electrolysis (Proton Exchange Membrane Electrolysis) is a technology that decomposes water (H₂O) into hydrogen (H₂) and oxygen (O₂) using electrical energy. It enables the production of high-purity hydrogen through electrochemical reactions and is characterized by fast reaction kinetics and high current density. Due to its compatibility with renewable energy sources, PEM electrolysis is regarded as a key technology for achieving carbon neutrality.
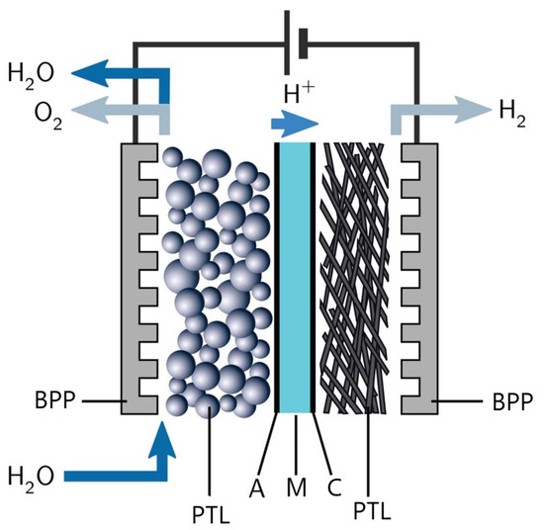
Currently, PEM electrolysis faces several technical challenges, including the use of expensive catalysts and components, high operational costs, and limited durability. In particular, when directly coupled with intermittent renewable energy sources, fluctuations in power input can lead to reduced electrochemical reactivity and decreased durability of the electrolyzer. These power variations dynamically affect internal physical conditions—such as temperature, pressure, and gas saturation—making them difficult to measure experimentally and requiring costly diagnostic equipment. Therefore, the development and advancement of physics-based numerical modeling and simulation technologies capable of precisely predicting these variables are essential.
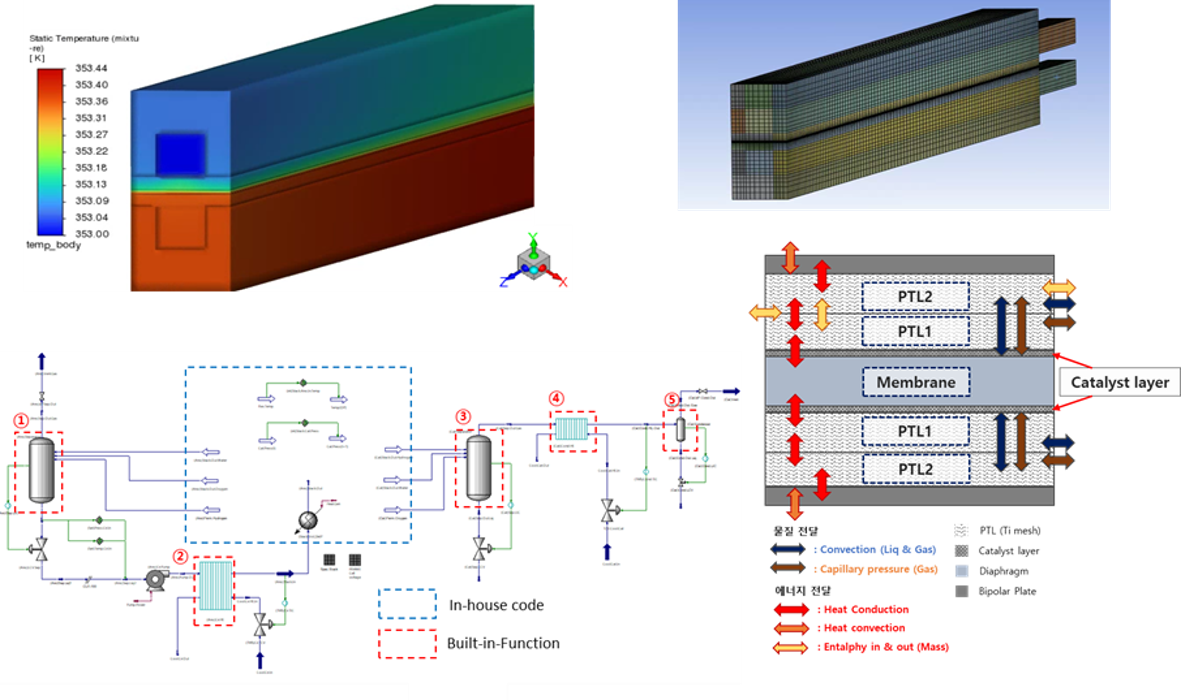
Our research group develops high-resolution simulations to calculate the spatial and temporal distribution of key internal parameters—such as temperature, pressure, and gas saturation—within the electrolyzer cell and systematically analyzes their effects on performance. We developed dynamic simulation models based on Simulink® and CFD models based on ANSYS Fluent® to reliably predict electrolysis behavior under various operating conditions. Furthermore, beyond stack-level modeling, we utilize process simulation tools such as Aspen Plus® and HYSYS® to support system-level design and control strategy development. These multi-scale modeling approaches enable diverse applications, including:
· Implementation of digital twins for real-time system behavior prediction
· Development of fault detection algorithms based on temporal comparison with observed data
· Derivation of control strategies and optimal operating conditions under dynamic power inputs
This integrated modeling framework plays a pivotal role in enhancing the reliability of PEM electrolysis systems and establishing robust operational strategies under real-world conditions.
Solid Oxide Electrolysis Cell (SOEC) stands out as a promising high-temperature electrolysis technology to achieve carbon neutrality, technologies that enable efficient hydrogen production and CO2 utilization are essential. Operating at elevated temperatures, SOEC reduces the thermodynamic barrier of electrolysis, achieving high efficiency by utilizing both electrical and thermal energy. SOECs convert steam or CO2 into hydrogen (H2) and carbon monoxide (CO) through electrochemical reactions, providing a clean and efficient route to syngas production for e-fuel and chemical synthesis. Furthermore, by leveraging hybrid thermo-electric integration, SOEC systems can effectively utilize waste heat and fluctuating renewable energy sources.
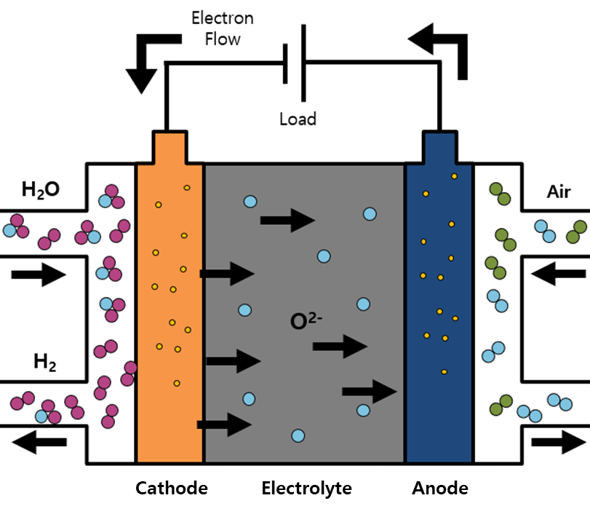
Despite its advantages, the commercialization of SOEC technology faces several challenges. Key issues include material degradation under high-temperature conditions, electrode delamination and pore structure collapse, and increased interfacial resistance during long-term operation. Phenomena such as Ni particle coarsening, cracking of ceramic electrolytes, and degradation of sealing materials can significantly deteriorate cell and stack performance. In addition, rapid changes in power input from renewable sources require dynamic system responses, demanding sophisticated control strategies and thorough modeling of mass and heat transport.
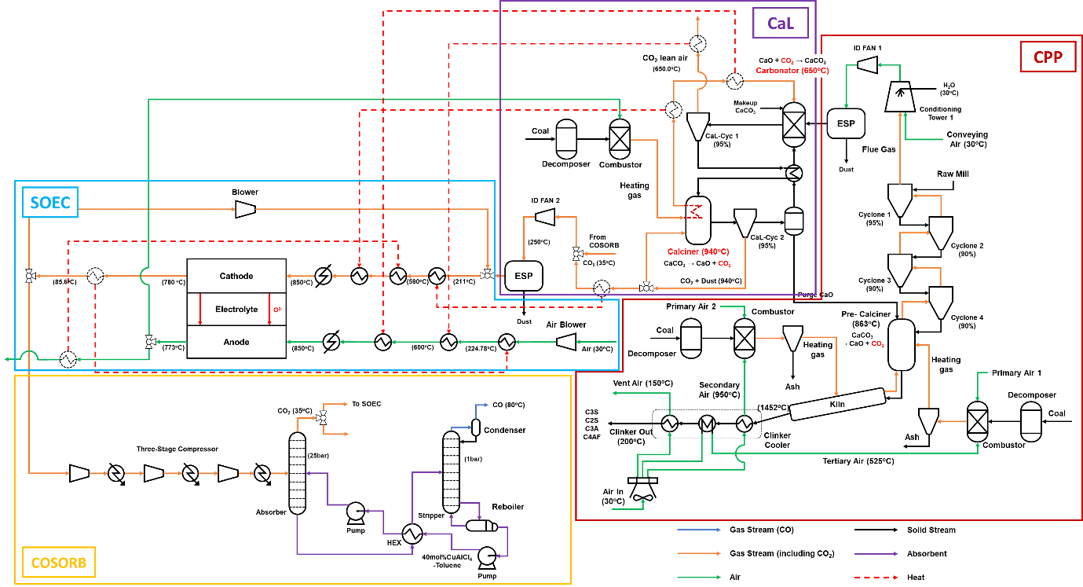
Our group focuses on developing dynamic SOEC system models and performing multi-physics simulations that capture electrochemical, thermal, and fluidic behaviors. In particular, we are investigating co-electrolysis of steam and CO2 to produce syngas (H2 + CO) as a precursor for synthetic fuels. Through CFD-based modeling (ANSYS Fluent®) and process integration (Aspen HYSYS®), we aim to:
· Analyze steam/CO2 electrolysis and co-electrolysis performance under dynamic operating profiles,
· Design heat-integrated SOEC systems applicable to industrial processes (e.g., cement plants), and
· Develop control strategies for variable input conditions such as intermittent renewable energy. In addition, we conduct techno-economic analysis (TEA) to assess the feasibility and optimization of SOEC deployment in industrial decarbonization scenarios.
Anion Exchange Water Electrolysis (AEMWE) is a technology that uses electricity to split water (H2O) into hydrogen (H2) and oxygen (O2). The AEMWE combines the strengths of other commercial water electrolysis types, alkaline water electrolysis and polymer electrolyte membrane water electrolysis. It is low cost due to use of non-noble metal catalysts such as nickel or iron-based materials, and it can produce high purity hydrogen. Additionally, AEMWE is suitable for wide range of water sources such as seawater. Due to these advantages, the AEMWE is gaining attention as a next generation water electrolysis technology.
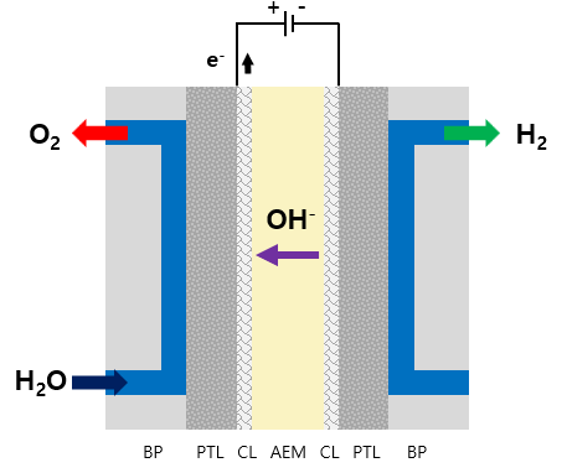
However, the technical readiness level of the AEMWE is low compared to the other commercial water electrolysis. Primary limitations are the insufficient durability and low performance of both the anion exchange membrane and the catalyst. As a result, there is no study of detailed stack and system, as well. These limitations cause a challenge to scale up the technology for industrial applications, highlighting the need for further development in material and modeling.
Our research group focuses on developing a highly reliable AEMWE stack and system model. In particular, we aim to solve the challenges of integrating the AEMWE systems into renewable energy sources in real environment. When the power is supplied from fluctuation energy, it affects performance, and durability of the AEMWE stack and system. Therefore, it is necessary to analyze response characteristics of the stack under the dynamic operating conditions. To achieve this, we developed a dimensional stack model based on the AMESim®, which enables the analysis of physical behaviors such as electrochemical reaction, temperature distribution, and mass transport. In parallel, a system level model was developed using Aspen Plus to evaluate the efficiency and system behavior under the various operating conditions. These multi-scale modeling using various simulation tool approaches following objectives:
· Development of strategies for enhancing efficiency and extending life span of the AEMWE system.
· Conduction of economic evaluation to estimate cost and commercial viability of the AEMWE.
· Establishment of a digital twin of the AEMWE system, which can be used in real-time to monitor and optimize the system performance.